一、设备参数
设备型号
|
SY-QFW355-SL
|
电源电压
|
380V/50Hz
|
气源压力
|
0.5~0.8Mp
|
主电机功率
|
7.5KW(依据材料而定)
|
主轴转速
|
2850rpm(支持变频调速)
|
最大切割宽度
| 80mm
|
最大切割高度
|
120mm
|
切割精度
|
±0.1mm
|
锯片冷却方式
|
微量润滑
|
锯片规格
|
Φ 350mm 向下兼容
|
送料伺服电机功率
|
1.5KW
|
锯切进刀伺服电机功率
|
1.5KW
|
尾料伺服电机功率
|
750W(无尾料设备具备)
|
吸尘器功率
|
5.5KW
|
单次送料长度
|
15-100mm(可循环往复送料)
|
设备外形尺寸
|
约3500*2000*1850mm
|
二、设备实拍
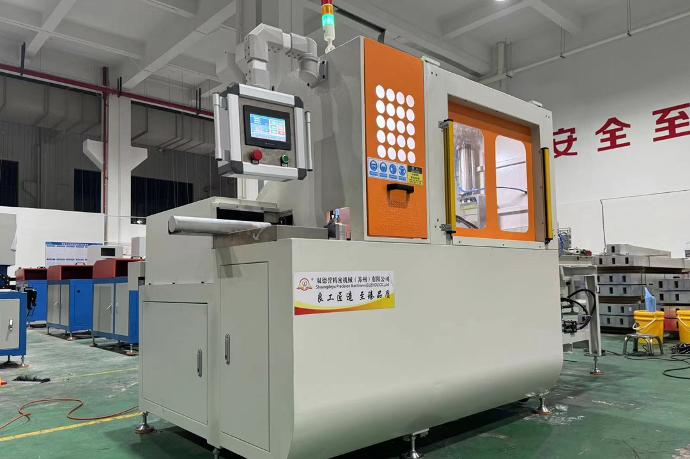
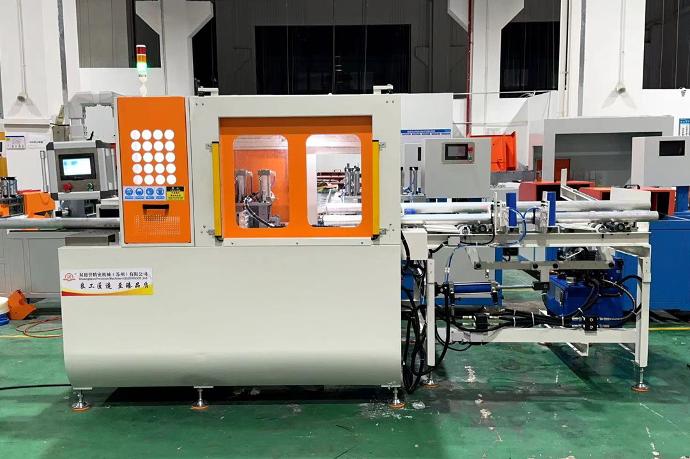
三、设备特点
1、 特殊工艺不伤材料:设备拥有自主发明防刮伤专利结构,工作台面无需加装任何防刮伤材料(如电木板,橡胶板等)任何铝型材在设备运动过程中不会因摩擦而拉伤材料表面;
2、 剩余尾料短:自主研发普通机型尾料可短至120mm,比同行业标准机型尾料缩短2倍以上,无尾料机型尾料可短至30mm,为广大用户大大节约材料成本;
3、 切割稳定精度高:全系列设备采用横向进刀方式,保证其切割稳定性;
4 、不同长度切割:全自动设备可实现同一根材料多段不同长度的切割,节约人工换料时间,伺服系统送料,送料精度稳定,效率更高;
5、 环保微量润滑系统:全系设备配备微量冷却润滑系统,可延长锯片使用寿命30%以上,切割材料表面光滑无毛刺,配备专业吸尘装置,让铝屑不再满天飞;
6、自动上料机构:具备储料15支圆棒,自动输送翻转带自动送料机构,此过程全部设备自动运行。
7 、设备整机接地,可有效避免漏电造成触电的安全隐患;
8、设备采用多吸尘口,配备大功率吸尘器,有效提高铝屑回收效率。